В 90-х годах прошлого столетия в энергетике России был осуществлен повсеместный переход с асбестовых уплотнений для арматуры на уплотнения из терморасширенного графита (ТРГ). В результате удалось существенно увеличить надежность сальников, при этом значительно снизилось число аварийных остановов энергоблоков по причине разгерметизации арматуры, что в свою очередь позволило увеличить межремонтный период ТЭС до 4 лет.
Уплотнение узла бесфланцевого соединения корпуса и крышки энергетической арматуры ― в среде специалистов ― «плавающей крышки», также было осуществлено с помощью графитовых колец ТРГ. Это нововведение позволило уменьшить высоту сальниковой камеры и существенно увеличить надежность соединения, поскольку основным недостатком применяемых ранее асбосодержащих уплотнений являлось двух- трехкратное уменьшение объема уплотнения и значительное снижение упругих свойств в процессе эксплуатации. Однако, поскольку несомненным преимуществом асбестовых уплотнений является их волокнистая структура, асбестовый сальник не выдавливается даже в большие зазоры сальниковой камеры.
Сальниковые уплотнения ТРГ, обладая лучшей упругостью, не высыхающие и не стареющие, склонны к экструдированию в зазоры, превышающие 0,02 ширины поля кольца под действием высокого давления. (Здесь нужно оговориться, что это все же не эффект хладотекучести, свойственный фторопласту, где уплотнение экструдируется при низких давлениях в крайне малые зазоры). Для исключения данного негативного свойства кольца ТРГ снабжают специальными противоэкструзионными элементами ― обтюраторами тарельчатого или углового типа, а размеры посадочных мест сальниковой камеры выполняют строго в соответствии с КД завода-изготовителя.
Неукоснительное соблюдение технологии изготовления энергетической арматуры, ее эксплуатации и ремонта позволили прожить до середины двухтысячных годов без особых претензий к арматуре, и, в частности, к герметичности «плавающей крышки», но дальше случаи выбивания сальника в данном узле стали регулярными.
Проблема, на наш взгляд, заключается в следующем.
В силу разных причин ― отсутствие финансирования, закуп арматуры на тендерной основе, повышение цен на новую качественную арматуру, снижение квалификации и количества ремонтного персонала – арматура в теплоэнергетике в последние годы почти не заменяется и при этом зачастую несвоевременно и некачественно ремонтируется. В связи с этим износ посадочных мест узла бесфланцевого соединения корпуса и крышки энергетической арматуры достигает критических значений.
Например:
• согласно конструкторской документации (КД) ЗАО «Энергомаш (Чехов) ― ЧЗЭМ», допуск для расточки корпуса Н11, что для диаметра 400 мм составит +0,36 мм;
• для бывшей в эксплуатации арматуры допуск на расточку корпуса увеличивается до Н13, согласно РД 153-34.1-39.605- 2002 «Общие требования и указания по применению уплотнений из терморасширенного графита в арматуре ТЭС», и для диаметра 400 мм допуск составит +0,89 мм;
• фактические значения диаметра расточки корпуса реально эксплуатируемой арматуры могут превышать номинал на 1,0–1,5 мм.
Примерно такая же картина складывается с размерами крышки и кольца опорного. Суммарно отклонения сопрягаемых деталей сальникового узла приводят к появлению зазоров, достигающих указанных выше значений в 1,0-1,5мм.
Разработанные в начале 90-х годов прошлого столетия отечественные кольца ТРГ, изготовленные по технологии прессования свернутой в рулон ленты ТРГ и оснащенные обтюраторами, легко обеспечивали требуемую надежность сальника при соответствии диаметра сальниковой камеры требованиям КД ЗАО «Энергомаш (Чехов) ― ЧЗЭМ», т.е. допуску на диаметр по Н11 и даже по Н13. При этом дальнейшее увеличение разности диаметра сальниковой камеры и диаметра прессованного кольца при обжатии приводит к его разрушению, поскольку при обжатии кольца внешние слои графитовой фольги испытывают растягивающие нагрузки и, не находя опоры на стенки корпуса, рвутся.
Защитные элементы ― угловые или тарельчатые обтюраторы, предотвращающие экструдирование колец ТРГ в зазор, не превышающий, согласно КД, двух процентов ширины поля кольца, выдавливаются вместе с графитом в «средние» по размеру зазоры и заклинивают плавающую крышку, либо проваливаются в «большие» зазоры полностью и никак не препятствуют выдавливанию графита из сальниковой камеры.
Таким образом, несоблюдение посадочных размеров узла плавающей крышки вновь выпускаемой арматуры, снижение технологической дисциплины эксплуатации и ремонта арматуры и ограниченные технические возможности традиционных колец ТРГ являются основными причинами участившихся случаев выбивания сальников ТРГ в узле «плавающей крышки» на арматуре высокого давления.
Применение мягких плетеных сальниковых набивок ТРГ, легко подстраивающихся под размер сальниковой камеры, в качестве уплотнения плавающей крышки на высоких и сверх- высоких параметрах крайне опасно из-за выгорания связующего и выдавливания набивки в зазор. Применение жестких углеродных набивок в качестве замыкающих колец также не рекомендуется, вследствие их разрушения от вибрации, сопровождающей работу всего энергетического оборудования, до отдельных микрофиламентов, которые легко продавливаются в зазоры и выдуваются потоком среды.
Для решения данной проблемы специалистами ООО «Силур» разработан сальниковый комплект, состоящий из колец ТРГ повышенной упругости и замыкающих элементов, обеспечивающих работоспособность сальника при больших зазорах.
На графике рисунка 1 показана способность колец ТРГ повышенной упругости и аналогичных колец с замыкающим элементом воспринимать сжимающие нагрузки и уплотняться без разрушения при наличии зазоров h до 1,7 мм. Схема нагружения представлена на рисунке 2. Схема испытания представлена на рисунке 3.
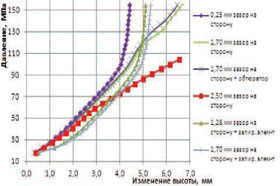
В таблице 1 представлены данные изменения наружного диаметра кольца без разрушения, под действием сжимающих нагрузок, для сальниковых колец 360х305х20, изготовленных по разной технологии.
Увеличение упругости сальниковых колец обусловлено повышенными механическими свойствами исходной графитовой фольги, в том числе: прочностью на разрыв > 6 МПа, относительным удлинением >3% и «ноу-хау» конструкции и способа изготовления колец. При этом сальниковое кольцо не имеет обтюратора, а предотвращают выдавливание в зазор замыкающие элементы в виде специальной прокладки с многослойным П-образным обтюратором.
Для проверки результатов стендовых испытаний и подтверждения работоспособности сальникового комплекта в рабочих условиях в период с января по август 2014 года на испытательной базе ЗАО «Энергомаш (Чехов) ― ЧЗЭМ» были проведены испытания сальниковых комплектов размером 170х145, состоящих из двух уплотнительных колец и трех замыкающих прокладок, расположенных по краям и в середине комплекта. Испытания проводились на двух макетах узла бесфланцевого соединения корпуса и крышки энергетической арматуры (Рисунок 4).
Макет №1
1. Диаметр расточки корпуса ― Дкор=170,8 мм;
2. Диаметр бурта крышки ― Дкр=168 мм;
3. Зазор ― h=1,4 мм.
Макет №2.
1. Диаметр расточки корпуса ― Дкор =171,3 мм;
2. Диаметр бурта крышки ― Дкр =168 мм;
3. Зазор ― h=1,65 мм.
Величина зазоров в макетах узлов превышает максимально допустимые величины зазоров на новую и находившуюся в эксплуатации арматуру:
Новая арматура, согласно КД ЗАО «Энергомаш (Чехов) ― ЧЗЭМ»:
1. Диаметр расточки корпуса ― Дкор =170,25 мм;
2. Диаметр бурта крышки ― Дкр =169,857 мм;
3. Зазор ― h=0,197 мм.
Бывшая в употреблении арматура, согласно РД 153- 34.1-39.605-2002:
1. Диаметр расточки корпуса ― Дкор =170,63 мм;
2. Диаметр бурта крышки ― Дкр =169,5 мм;
3. Зазор ― h=0,565 мм.
Испытания проводились при давлении 30,0 МПа и температуре 300°С. Выполнено по 100 циклов подъема и сброса давления. В обоих случаях сальник остался герметичным. Состояние сальника в макете №1 можно считать удовлетворительным, но в макете №2 обтюратор был полностью выдавлен в зазор, а нижнее кольцо имело облой 8 мм, что не может считаться приемлемым. Описание состояния комплектов после испытаний приведено в таблице 2.
Выводы:1. Уплотнительные кольца ТРГ производства ООО «Силур», выполненные по новой технологии, действительно способны упруго расширяться без разрушения под действием сжимающих нагрузок и могут быть рекомендованы для применения в расточке корпуса с отклонением по диаметру до 1,3-1,5 мм, в частности для диаметров до 180 мм по Н15, свыше диаметра 180 мм по Н14.
2. Комплект с замыкающими прокладками с П-образным обтюратором можно рекомендовать для герметизации сальниковых камер с зазором до 1,0 мм;
3. При зазорах больше 1,0 мм необходимо дополнительно использовать стальное подкладное кольцо толщиной 3,0 мм с диаметральным размером меньше диаметра расточки корпуса на 0,7–1,5 мм.
Опубликовано в "Вестнике арматурщика"№2 (22) 2015
Размещено в номере: "Вестник арматурщика" № 2 (22) 2015